- Textile Accessories
- Shuttle Loom Parts
- Textile Equipment
- 1511 Textile Machine Parts
- 1515 Textile Machine Parts
- GA615 Shuttle Loom Parts
- Textile Hardware And Tools
- Weaving Machinery
- Textile Auxiliary Equipment
- Textile Picker and Buffer
- Textile Wooden Parts
Installation Instructions For The Dot Pecking Type Weft Deficient Self Stopping Device
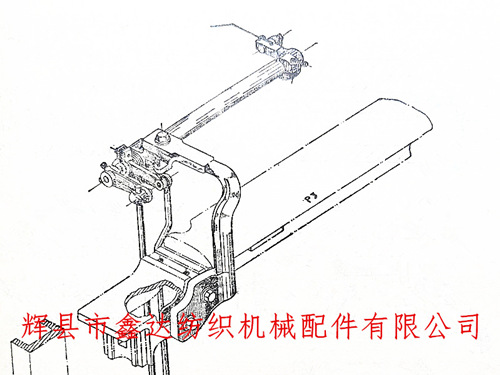
The point pecking type missing weft self stopping device, also known as the anti hundred foot device or the broken weft stopping device, is a measure taken in China to improve the quality of cotton fabric. There are various types of devices, such as the weft fork and the gantry stop for broken weft, the point pecking type broken weft stopping device, and the photoelectric induction broken weft stopping device. The point pecking type is widely used, and the weft is inspected once during each beating, and the detection point is within the range of the fabric width. Therefore, it has better detection effect on preventing "hundred foot" and double weft defects in multi page woven fabrics than the three finger fork (weft fork). Here are the installation instructions for the device:
1. Position of the pecking type triple tube:
(1) The vertical distance between the bottom edge of the three sleeves and the fabric surface should be controlled between 47-50 millimeters.
(2) The horizontal distance between the back edge of the triple tube and the chest beam is 80 millimeters.
(3) When installing the rocker arm, attention should be paid to leaving appropriate clearance between the connecting rod and the front brake rail screw core K41, as well as the shuttle box cover plate support foot K201, and avoiding collision.
2. Adjust the needle holder and needle position:
(1) When the bending axis is below the front center and the distance between the reed and the chest beam is 210 millimeters, the needle tip is 8-10 millimeters away from the weaving mouth, and the gap between the needle seat and the middle sleeve is 0.5-1 millimeter. The height of the needle tip should be adjusted to be about to contact the upper warp yarn. The steel needle is required to swing flexibly from side to side, and the lifting distance of the needle seat should not be too large when it meets.
(2) Needle tip swing amplitude: 12-15 millimeters (the thickness of the steel needle is selected according to the fabric, with general specifications of 0.8mm, 1.0mm, and 1.2mm).
(3) When the bending axis is at the front dead center, that is, the steel needle is in the starting low position, and the needle tip cannot touch the reed. The distance between the upper bend and the reed is 1-2 millimeters, and the distance between the lower needle tip and the reed is within 0.50 millimeters. The needle tip is inserted into the cloth 10-12 millimeters. If it is too deep, it will cause a needle path.
3. Calibrate the shutdown mechanism:
Rotate the bending axis of the weaving machine so that the needle seat meets the groove of the middle sleeve, and check the closing amount of the closing link, preferably 1.60 millimeters.
The instructions for the dot pecking type weft stop and the installation method for the missing weft self stop can facilitate the quick installation and calibration of this device by mechanics or maintenance workers. Welcome to exchange and share!